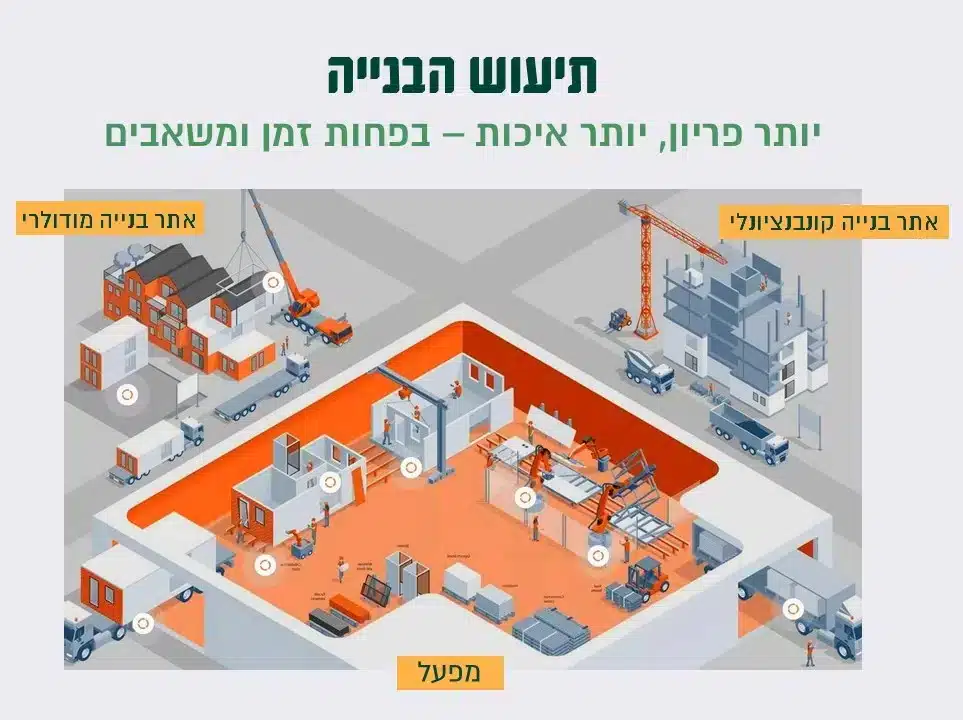
What precisely is modular construction?
It’s a method rooted in constructing tall buildings using pre-assembled modular units finished in factories. In contrast to prefab construction, these modules come fully equipped from the factory, complete with steel frame elements, interior fittings, and systems. On-site work is minimized to assembly and connecting systems using a plug-and-play approach.
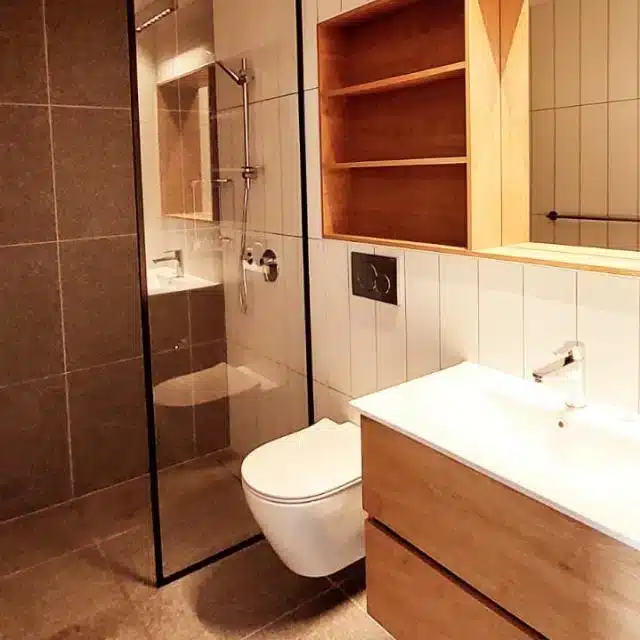
Pod & Modular apartment units
We specialize in two main products: pods, which serve as complete bathrooms, and modular apartment units that can operate either independently or as components of larger apartments. Both are manufactured in a factory using the modular construction method. Once completed, they are delivered to the construction site fully equipped and ready for connection. Developers or contractors have the flexibility to customize finishes according to their preferences, and their integration into a project is similar to assembling furniture.
Both products offer significant advantages for projects requiring multiple identical room types, such as student dormitories, hotels, retirement communities, and nursing homes. However, recent efforts have also been made to introduce them into residential construction projects.
Installation occurs in two ways:
For pods, the only essential tasks for full functionality entail connecting them to hot water, cold water, sewage, and electricity lines.
For modular apartment units, beyond linking the aforementioned main systems, we also connect the unit to the conventional core of the building, which acts as the primary supporting system.
Thanks to the rigorous design and production processes at the factory, on-site installation is swift, typically taking just several hours under the close supervision and guidance of factory staff.
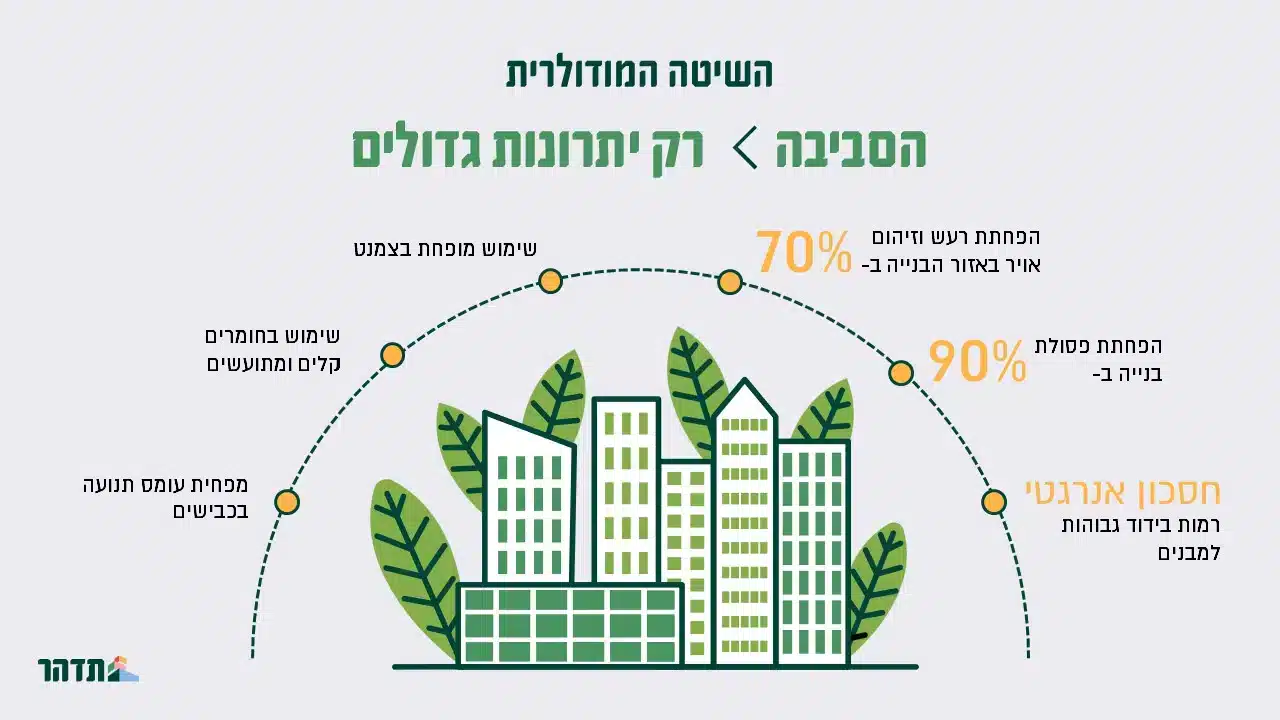
The modular method
The advantages are manifold: the modular method fosters a clean construction process without the need for extensive on-site labor and machinery, reducing dust, concrete usage, metal waste, and leftover materials. In this regard, modular construction significantly contributes to mitigating the detrimental environmental impact associated with traditional real estate practices, which are among the leading contributors to pollution. Since it primarily involves dry construction activities, on-site operations have minimal environmental repercussions.
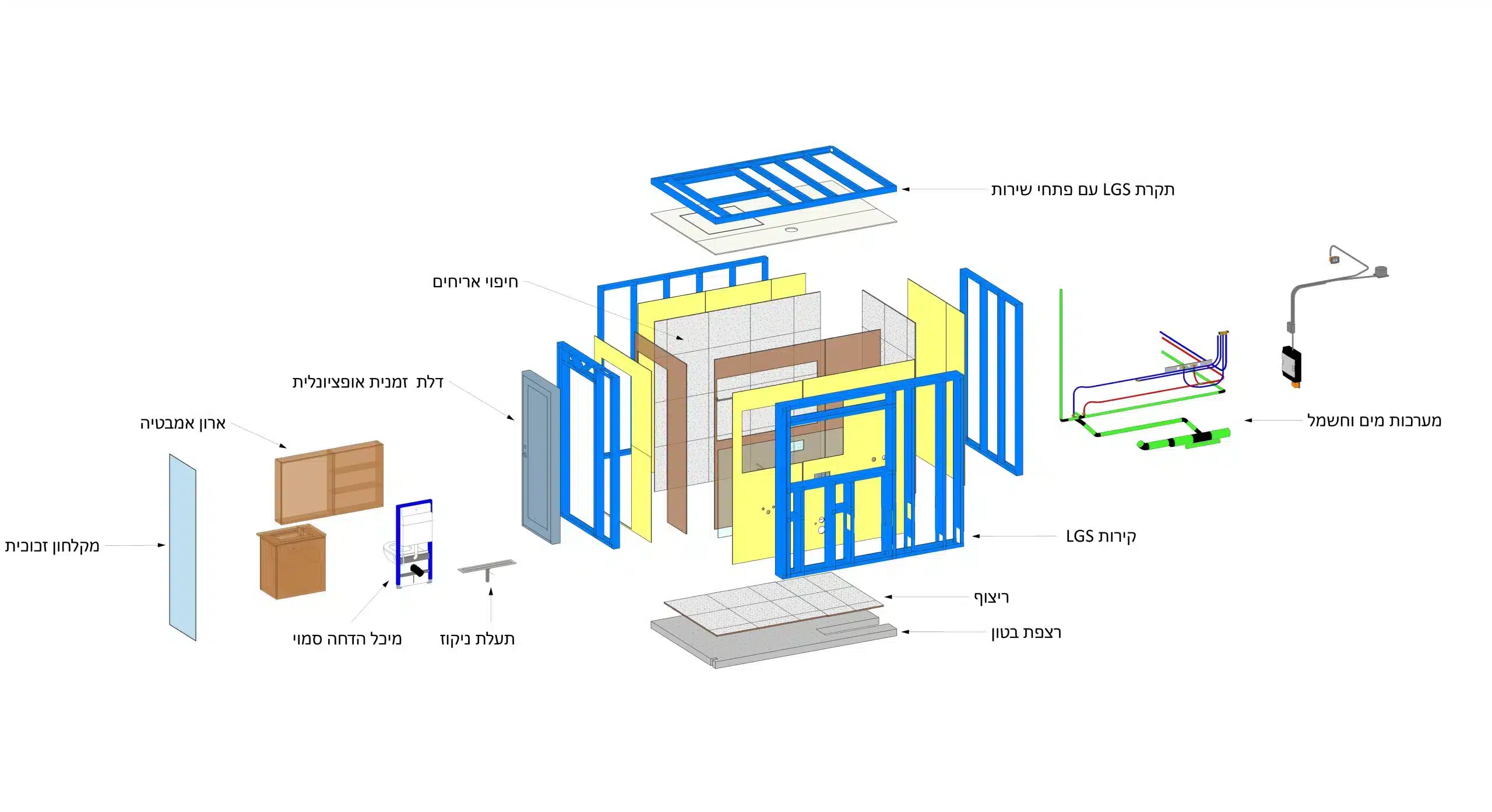
The planning process
Our objective is to establish an efficient workflow, commencing from the planning phase through the transition to factory production, where 3D units are manufactured via assembly line methods, and concluding with their on-site assembly. Presently, pod projects are meticulously planned within the Tidhar planning department. Planning responsibilities are delegated to the VDC (Virtual Design and Construction) department, where a comprehensive production plan is formulated down to the minutest detail, akin to assembly instructions from IKEA. This meticulous planning minimizes room for individual interpretation among workers, as variations in execution can lead to errors and diminished quality. As part of the unit planning process, products and methodologies are integrated to reduce reliance on individual interpretation.
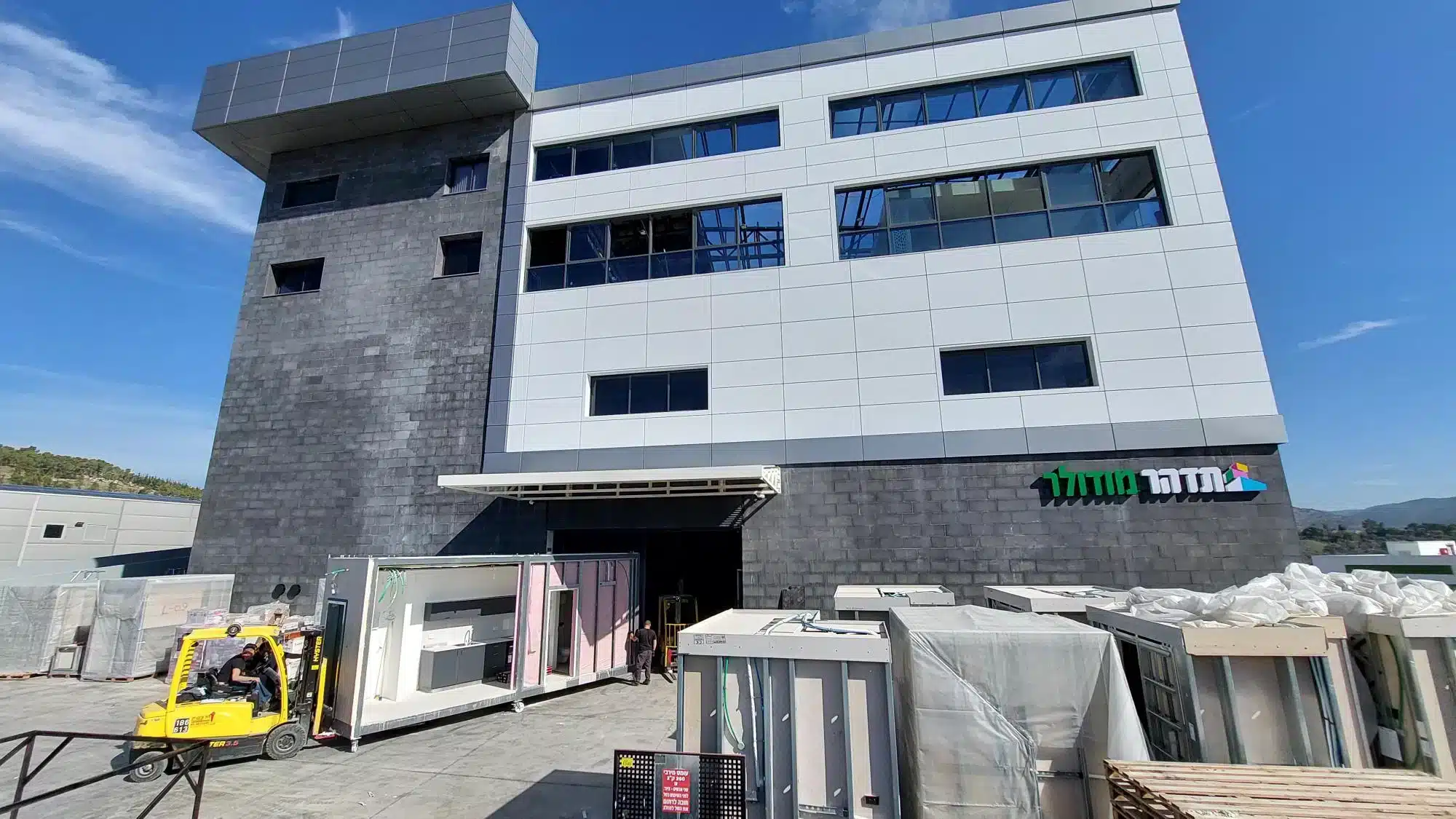
The Supervisory Process
We allocate significant resources to ensure the delivery of impeccable, ready-to-use products to our customers, assuming responsibility for every stage of the process, from floor casting to the conclusion of inspection and warranty periods. Each apartment leaving our factory undergoes rigorous quality control. With constant professional oversight at every production stage, we achieve exceptionally high-quality, durable, and precise results surpassing those attainable through conventional on-site construction methods. This approach also eliminates defects, cost overruns, and unforeseen expenses stemming from errors, theft, on-site accidents, adverse weather conditions, labor shortages, or coordination issues between suppliers and professionals. The resulting product is innovative, environmentally friendly, and of superior quality, while yielding substantial resource savings.
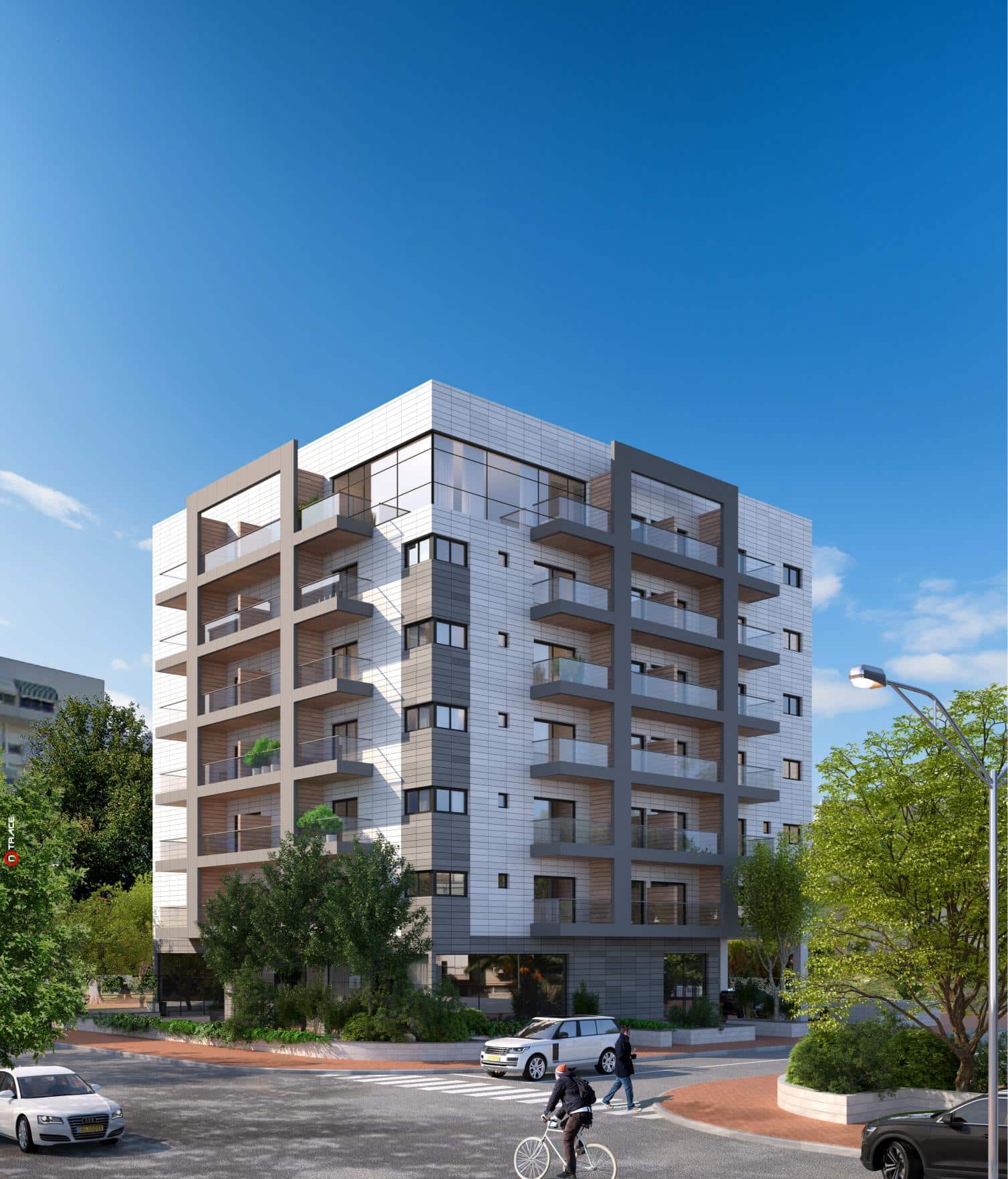
The Etrog Ashdod project
Etrog Ashdod represents Israel’s inaugural high-rise modular construction venture. This residential building comprises six stories above a ground floor and parking level, encompassing 75 apartments. While the parking lot, ground floor, and structural core with elevators and safe rooms were constructed conventionally, all 75 apartments were fully assembled at Tidhar’s factory in Yavne before being brought to the site and installed using the plug-and-play approach. Etrog Ashdod is a residential initiative of the Ministry of Construction & Housing, intended for long-term rental to eligible applicants.
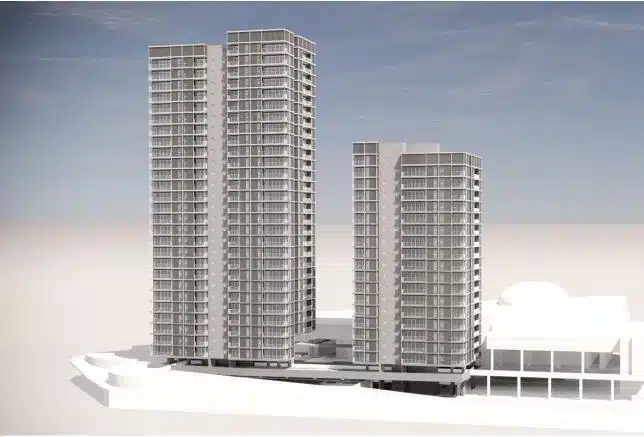
The Castra Haifa project
Several other projects by Tidhar are currently in the planning stages, with Castra Haifa being a notable endeavor. This project will feature 320 apartments available for long-term rental to the public. It comprises a 20-floor tower and a 30-floor tower atop the existing Castra Mall, offering a selection of 2, 3, and 4 BD apartments.
Talk to us
We invite you to contact us:
